射出成形機は完成しましたが、本番はこれから。
なにぶん射出成形というものを自分でやったことが無く、感覚が分かりません。
まずは光造形方式の3Dプリンターで作った型で試してみることにしました。
樹脂を溶かして重ねていく積層式の場合は、熱で樹脂がやわらかくなるので、熱で溶かした樹脂を射出する、射出成形とは相性が悪い。光造形方式の場合は、UV光で硬化するレジンを使用するため、精度が良く、熱にも強いため、今回のような用途には向いています。しかし、樹脂は樹脂、強度不足が予想されるので、レジンも高靱性レジンを使用します。取扱の関係で、水性レジンをいつも使っているのですが、水性の高靱性レジンはバカ高い。
あんまり失敗は許されない。
とは言っても試してみなければ分からないので、試してみます。
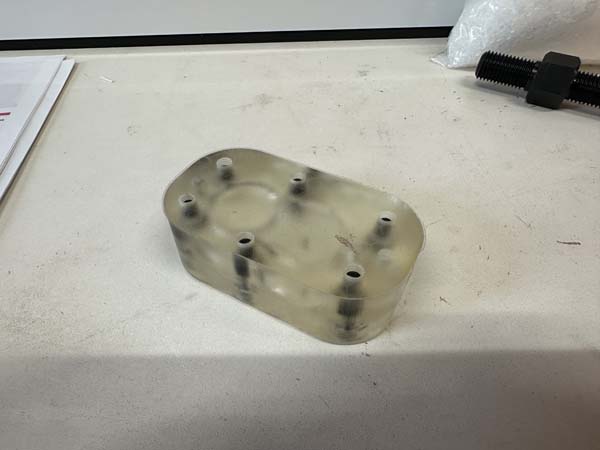
というわけで、型を作ってみました。
射出成形したところ・・。
バキッと割れてしまいました。
予想以上に圧がかかっているようです。
型の固定するボルトを増やしたり、射出成形の条件を変えたりして、色々試した結果・・。
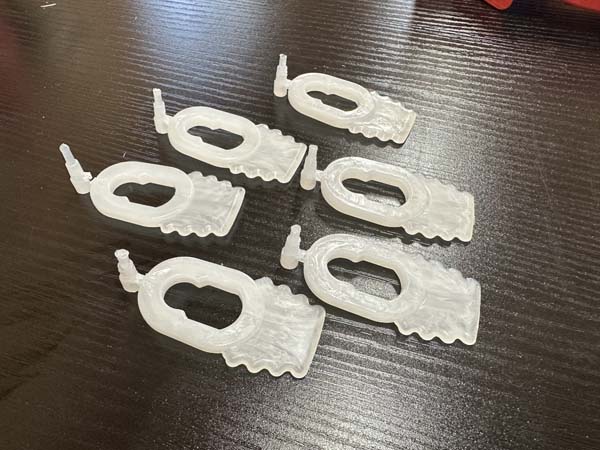
なんとか形になってきました。
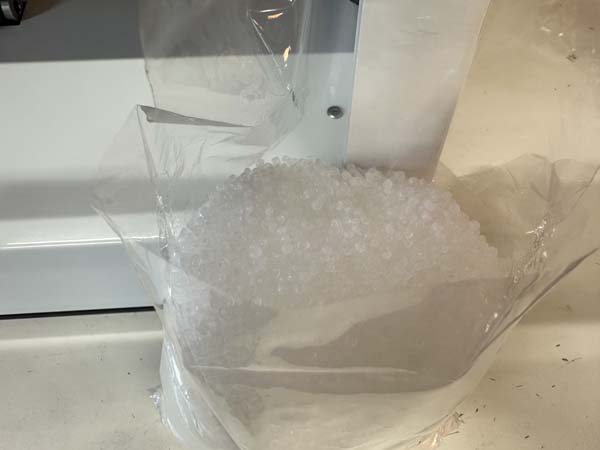
ちなみにペレットは手芸用として売っていたポリプロピレン。
お試しとしては比較的安く、問題無さそうです。
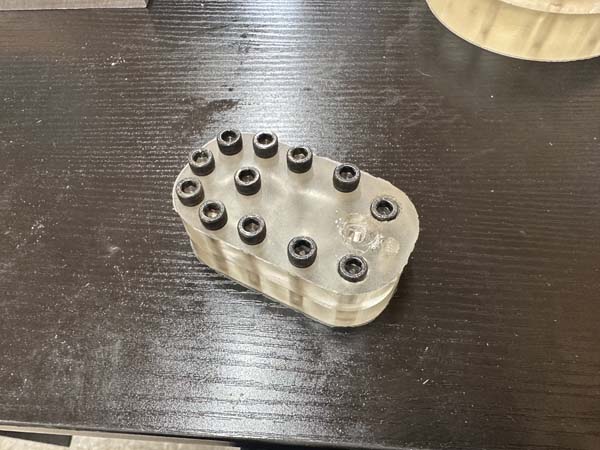
樹脂型は結局ずいぶんなストロング仕様になりました。
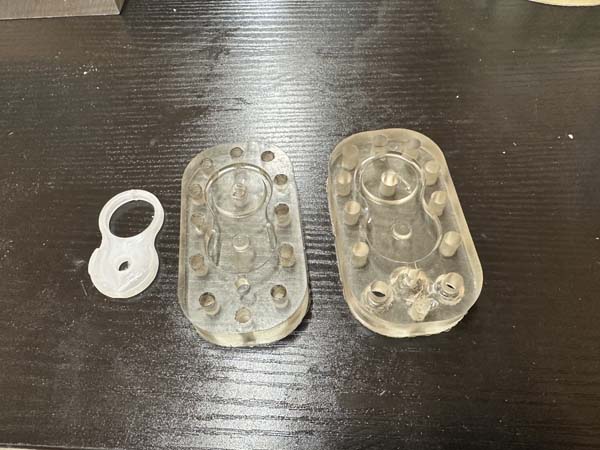
もう一種類のパーツも成型できるようになりました。
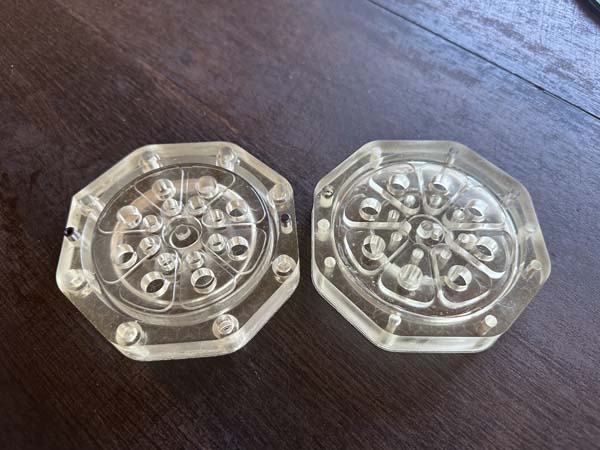
苦労したのはホイール状の部品。今回の成形機ではほぼ上限に使い体積です。
ここまで大きくなるとかかる圧力も半端なく、型はベシベシ割れて、まともな成形品ができません。
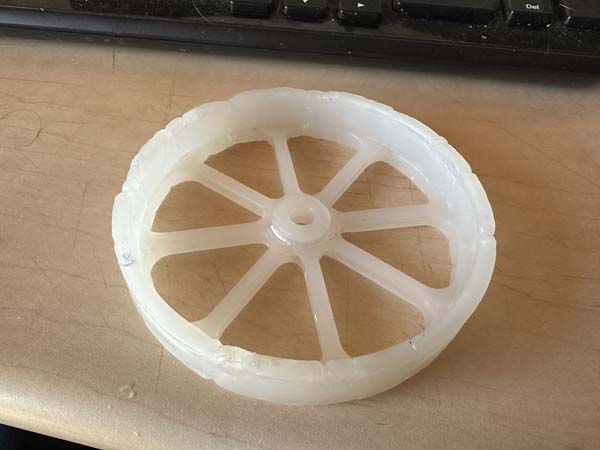
結局ボルト28本使用したストロング仕様となりましたが、これでも圧をあまり上げられず、綺麗なホイールはできませんでした。
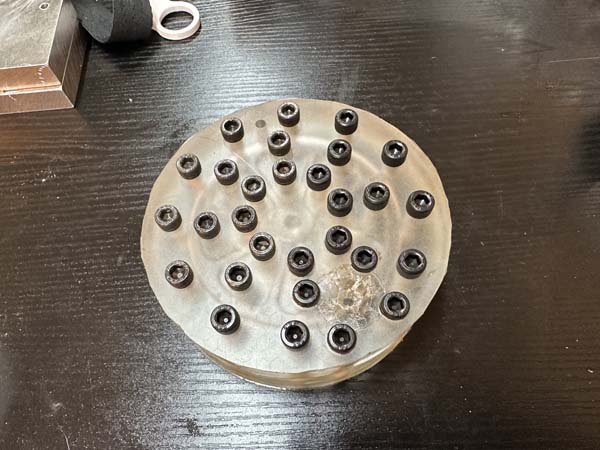
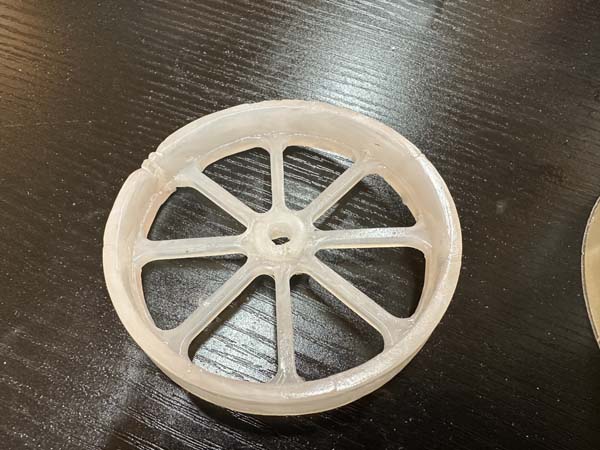
ただ、ゲート位置などのデータは取れたので、アルミの型製作に入りたいと思います。
製品製作に使うとなれば、ボルトの着け外しだけても大変なので、少し工夫が必要ですね。